Comprehensive Guide: What is Porosity in Welding and Exactly How to stop It
Comprehensive Guide: What is Porosity in Welding and Exactly How to stop It
Blog Article
The Science Behind Porosity: A Comprehensive Overview for Welders and Fabricators
Understanding the intricate mechanisms behind porosity in welding is essential for welders and fabricators aiming for flawless craftsmanship. As metalworkers explore the depths of this sensation, they uncover a world governed by various elements that influence the formation of these small spaces within welds. From the composition of the base products to the complexities of the welding process itself, a wide variety of variables conspire to either intensify or alleviate the presence of porosity. In this comprehensive overview, we will decipher the scientific research behind porosity, exploring its impacts on weld top quality and introduction advanced techniques for its control. Join us on this journey with the microcosm of welding blemishes, where precision satisfies understanding in the quest of remarkable welds.
Recognizing Porosity in Welding
FIRST SENTENCE:
Assessment of porosity in welding discloses important understandings right into the integrity and quality of the weld joint. Porosity, defined by the existence of tooth cavities or spaces within the weld metal, is a common issue in welding procedures. These gaps, if not properly addressed, can endanger the architectural honesty and mechanical residential properties of the weld, bring about prospective failures in the ended up item.
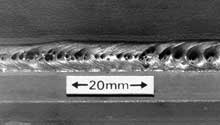
To spot and quantify porosity, non-destructive screening techniques such as ultrasonic screening or X-ray inspection are often employed. These techniques enable the identification of inner flaws without endangering the stability of the weld. By evaluating the dimension, shape, and distribution of porosity within a weld, welders can make informed choices to enhance their welding processes and attain sounder weld joints.
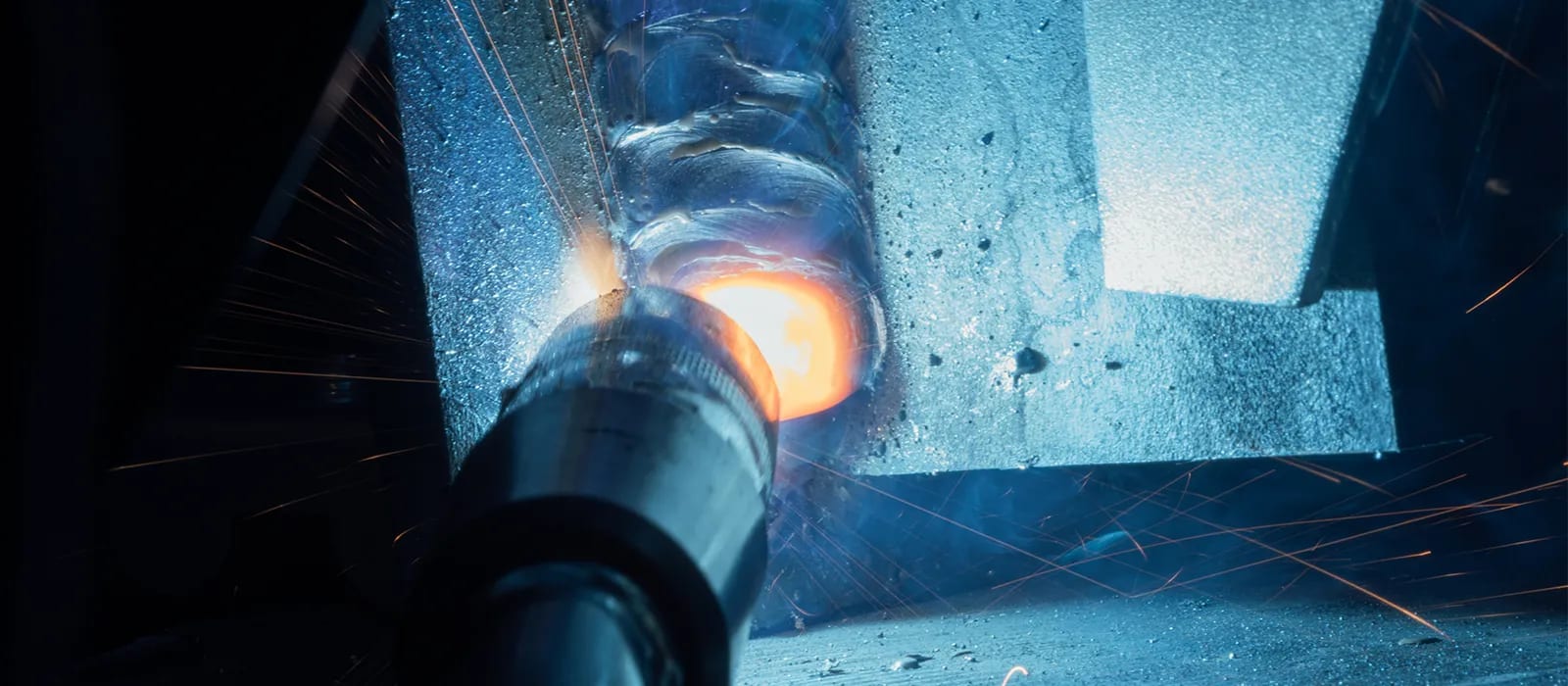
Elements Influencing Porosity Development
The event of porosity in welding is influenced by a myriad of aspects, varying from gas shielding performance to the intricacies of welding specification settings. Welding specifications, consisting of voltage, existing, travel speed, and electrode type, likewise effect porosity development. The welding technique employed, such as gas metal arc welding (GMAW) or protected steel arc welding (SMAW), can affect porosity formation due to variations in warm distribution and gas protection - What is Porosity.
Impacts of Porosity on Weld Top Quality
Porosity development significantly jeopardizes the architectural integrity and mechanical residential properties of bonded joints. When porosity is existing in a weld, it creates voids or cavities within the material, minimizing the general toughness of the joint. These spaces serve as anxiety focus factors, making the weld extra at risk to cracking and failing under tons. The existence of porosity likewise compromises the weld's resistance to corrosion, as the trapped air or gases within deep spaces can respond with the surrounding setting, bring about degradation over time. you could try here Additionally, porosity can hinder the weld's capacity to stand up to pressure or effect, additional jeopardizing the general top quality and reliability of the welded structure. In vital applications such as aerospace, vehicle, or structural buildings, where safety and security and resilience are critical, the damaging results of my blog porosity on weld quality can have serious repercussions, highlighting the relevance of minimizing porosity through appropriate welding methods and procedures.
Methods to Reduce Porosity
To boost the top quality of welded joints and guarantee structural integrity, welders and fabricators use certain methods targeted at decreasing the formation of gaps and cavities within the product during the welding procedure. One effective technique to reduce porosity is to ensure proper product preparation. This includes thorough cleansing of the base metal to remove any kind of pollutants such as oil, grease, or moisture that can contribute to porosity development. Furthermore, using the appropriate welding specifications, such as the appropriate voltage, existing, and travel rate, is critical in preventing porosity. Keeping a constant arc size and angle during welding additionally helps in reducing the probability of porosity.

Moreover, selecting the right protecting gas and keeping proper gas flow prices are essential in lessening porosity. Making use of the appropriate welding method, such as back-stepping or using a weaving motion, can also assist disperse warmth evenly and decrease the possibilities of click reference porosity development. Making sure appropriate air flow in the welding environment to eliminate any kind of possible sources of contamination is essential for attaining porosity-free welds. By applying these methods, welders can effectively lessen porosity and generate high-quality welded joints.

Advanced Solutions for Porosity Control
Executing sophisticated technologies and cutting-edge methods plays an essential role in accomplishing premium control over porosity in welding processes. In addition, employing sophisticated welding techniques such as pulsed MIG welding or customized environment welding can additionally help alleviate porosity issues.
One more sophisticated remedy involves the use of sophisticated welding tools. As an example, using tools with integrated attributes like waveform control and advanced source of power can improve weld high quality and lower porosity threats. The execution of automated welding systems with specific control over criteria can significantly minimize porosity flaws.
Furthermore, incorporating innovative monitoring and examination technologies such as real-time X-ray imaging or automated ultrasonic testing can help in detecting porosity early in the welding procedure, allowing for prompt rehabilitative activities. On the whole, integrating these innovative remedies can substantially enhance porosity control and boost the overall quality of welded elements.
Verdict
In conclusion, comprehending the science behind porosity in welding is important for welders and producers to generate high-grade welds - What is Porosity. Advanced solutions for porosity control can further boost the welding procedure and guarantee a strong and dependable weld.
Report this page